The Science of Inspections: From Data Collection to Predictive Insights
- Sam Fawzi
- Nov 29, 2024
- 4 min read
Updated: Dec 2, 2024
In the realm of operational efficiency, inspections are the cornerstone of maintaining equipment health, ensuring safety, and preventing costly downtime. However, traditional inspection methods often fall short of delivering the actionable insights needed to drive improvements. While organizations rely on manual processes or isolated systems, the real challenge lies in analyzing this data effectively without requiring excessive manpower or time.
We’ve addressed this challenge by developing a next-generation Inspection Tool that revolutionizes how data is collected, analyzed, and used for decision-making. This tool bridges the gap between manual inspections and predictive insights, ensuring organizations stay ahead of potential issues—all while empowering managers to create custom workflows and tailoring forms for field staff at specific locations.
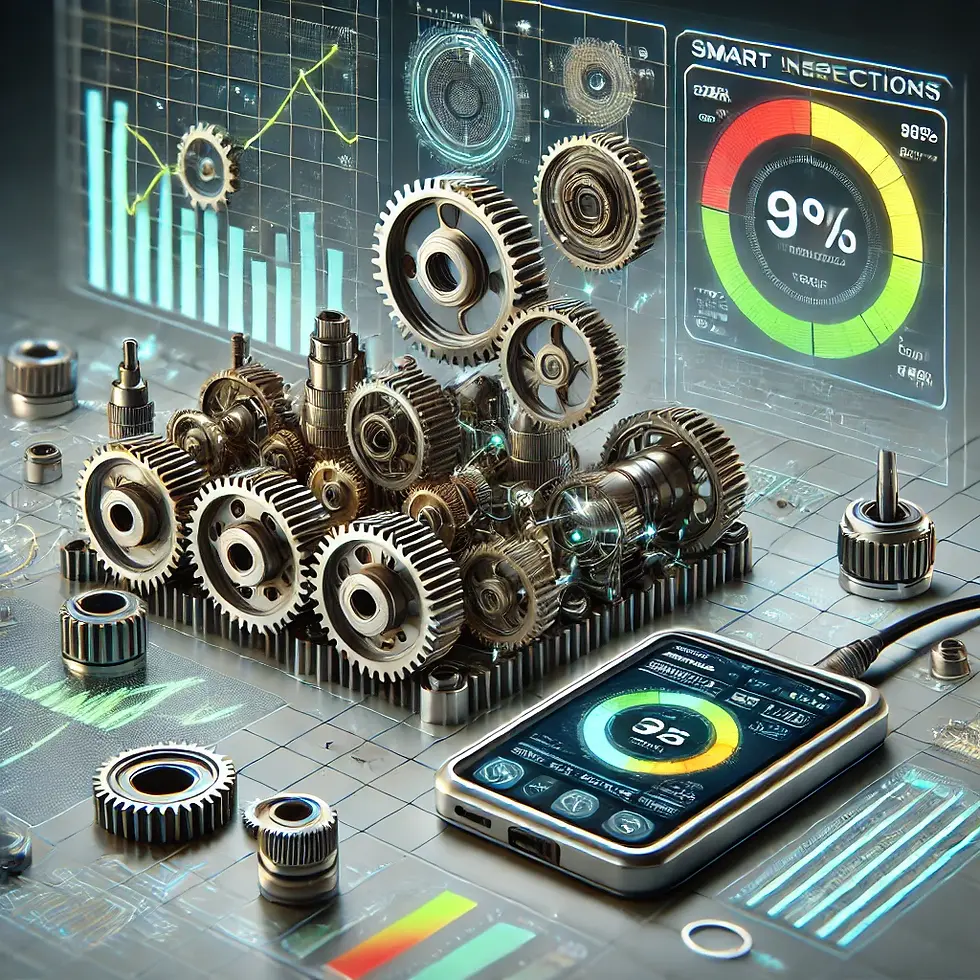
The Gaps in Traditional Inspection Methods
For many organizations, inspection data collection is still a largely manual process, relying on paper forms or Excel sheets. These traditional methods present several challenges:
Data Silos: Inspection data often remains isolated, with no centralized system to process and analyze it.
Time-Consuming Analysis: Extracting meaningful insights requires significant time and manpower, making it difficult to identify trends or anomalies.
Missed Opportunities: Without automated analysis, critical insights like performance trends, deviations, and early warnings remain buried in raw data.
Limited Flexibility: Static forms make it difficult to adapt inspections to the unique requirements of different locations, projects, or equipment types.
The Need for Predictive Analysis
Inspections are no longer just about identifying what’s happening now—they are about anticipating what could happen next. Predictive analysis allows organizations to:
Identify Trends: Spot gradual performance deterioration before it leads to failures.
Prioritize Maintenance: Allocate resources more effectively by addressing the most critical issues first.
Enhance Safety: Proactively mitigate risks by acting on anomalies early.
To achieve these outcomes, businesses need a tool that combines real-time data collection with automated analysis, eliminating the manual burden while delivering actionable insights.
Our Solution: A Smarter, More Flexible Inspection Tool
Recognizing these challenges, we built a Smart Inspection Tool designed to:
Empower managers to create and customize inspection forms.
Ensure field staff access only the forms specific to their working location.
Provide automated, real-time analysis of collected data.
Deliver predictive insights to support proactive decision-making.
Key Features of the Tool
Manager-Created Questionnaires
A Master Questions List serves as a centralized repository of inspection questions categorized by equipment type.
Managers can design custom inspection forms tailored to the unique needs of each project, location, or equipment type.
Each form can include specific questions based on local requirements, ensuring inspections remain relevant and efficient.
On-the-Fly Data Analysis
The tool calculates Lower Control Limits (LCL) and Upper Control Limits (UCL) dynamically based on historical data.
LCL and UCL are statistical thresholds that help identify whether equipment is operating within acceptable performance ranges. Readings outside these limits signal potential issues, enabling proactive responses.
Equipment-specific maximum and minimum specifications are integrated into the analysis, ensuring compliance with operational standards.
Real-Time Alerts: When readings fall outside acceptable ranges (e.g., above UCL or below LCL), automated alerts are sent to designated personnel for immediate action.
Trend Monitoring
The tool visualizes trends over time, highlighting gradual changes that may indicate potential failures.
This allows teams to address issues before they escalate, reducing downtime and maintenance costs.
Customizable Workflows
Managers can update forms and workflows as project or location needs change, ensuring the tool remains adaptable over time.
Why Control Limits Matter
Control limits, including Lower Control Limits (LCL) and Upper Control Limits (UCL), are critical for interpreting inspection data. They are calculated using statistical methods based on historical performance and help differentiate between normal variations and significant deviations. Industries such as manufacturing, healthcare, and energy rely heavily on these limits to:
Detect Anomalies Early: Identify potential issues before they escalate.
Ensure Compliance: Maintain equipment performance within regulatory and operational standards.
Drive Predictive Maintenance: Use trends and patterns to anticipate failures and optimize resource allocation.
By embedding control limit analysis into our tool, we ensure that every inspection delivers actionable insights in real-time.
How It Works
Questionnaire Creation
Managers log into the tool and design inspection forms by selecting questions from the master list.
Forms are assigned to specific locations, ensuring field staff have access only to the forms relevant to their site.
Data Collection
Field personnel use the tool to log equipment readings during inspections. The tool supports both mobile and desktop interfaces for seamless use in any environment.
Automated Analysis
Each reading is analyzed in real time, with the tool comparing data against:
Control Limits: Dynamically calculated LCL and UCL thresholds.
Specifications: Manufacturer-defined maximum and minimum acceptable values.
Anomalies trigger immediate notifications, allowing quick resolution.
Trend Visualization
Intuitive dashboards display performance trends, helping teams monitor equipment health and identify patterns over time.
Insights from these trends enable predictive maintenance and better resource allocation.
Advantages of Our Inspection Tool
Empowered Managers
Managers can design forms that cater to specific equipment types, locations, or projects, ensuring inspections are relevant and comprehensive.
Streamlined Workflows for Field Staff
Field personnel only see forms assigned to their location, simplifying the inspection process and ensuring consistency.
Automated Insights
Say goodbye to manual number-crunching. The tool delivers real-time analysis, saving time and manpower.
Full Data Ownership
Unlike proprietary systems, all data remains accessible to the organization for:
Advanced analytics and reporting.
Integration with other systems.
Repurposing for new processes or projects.
Proactive Maintenance
By identifying trends and anomalies early, the tool helps prevent costly breakdowns and ensures safety compliance.
Scalability for Growth
Supports multiple sites and projects, providing centralized visibility across the organization.
Conclusion
Inspections are no longer just about compliance—they’re about leveraging data to improve efficiency, reduce downtime, and enhance safety. Our Inspection Tool takes this a step further by automating the analysis process, providing actionable insights, and enabling predictive maintenance. With dynamic questionnaires, location-specific assignments, real-time control limit analysis, and comprehensive trend monitoring, this tool empowers organizations to make smarter, faster decisions.
Interested in transforming your inspection process? Contact us today to learn how our tool can meet your unique needs.
Comments